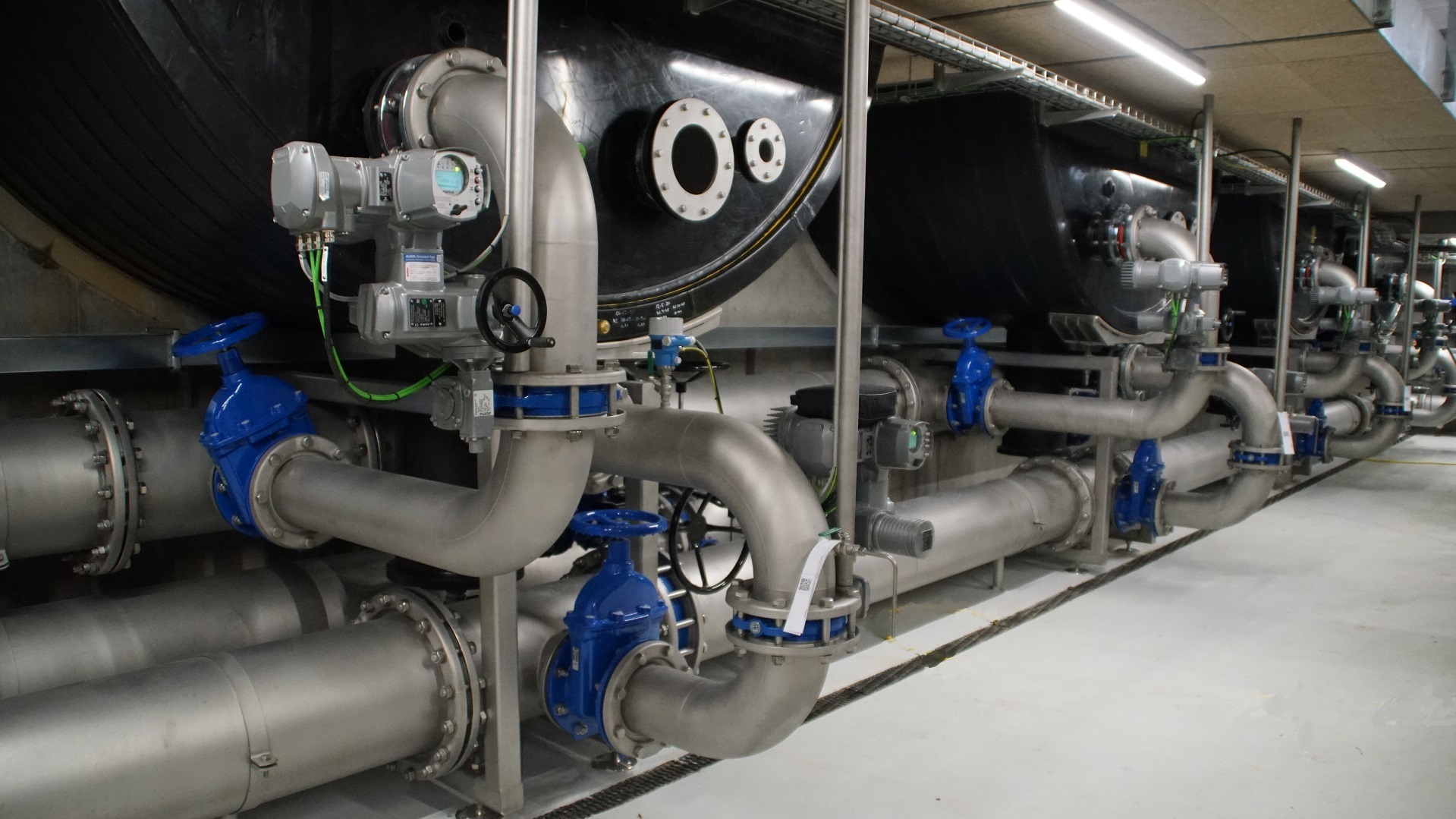
At Kasted water works outside of Aarhus, Denmark, a new facility has been established with the purpose of securing a future-safe water supply for the area.
The idea behind the facility is to reach a water supply that is tailored to fit the actual real-time demand, improve the staff’s work conditions and obtain the safest drinking water possible.
The facility holds six XL PE pipe water tanks with a total capacity of 2,000 m3. It replaces a previous installation with a single water tank made from concrete. Working with only one tank is risky, as maintenance or contamination could mean a temporary disruption of the supply to customers. Further, constructions made from concrete cracks over time, and damages are difficult to detect.
Plastic materials, such as PE, on the other hand are able to bend, and are cheaper in production, which was a further advantage while wanting to build six separate tanks. Having multiple tanks creates more flexibility, as maintenance or cleaning can be undergone without any interruption of the essential supply. Also, it is preferred to have as little stagnant water as possible, but to keep the water’s journey from ground to consumer as short as possible.
Full focus on high-quality drinking water
The water works produce more than 250 m3/hour all day from water drillings nearby, which is then filtered and oxygenated before it is sent off to the water tanks. The main purpose of the tanks is then to store enough water to assure a continuous supply and, while doing so, keep out any contaminating dirt or bacteria from the surrounding soil. Therefore, the tanks have an extra layer added on the outside, and the gap between the inner and outer layer is filled with pressurized air. This makes it possible to monitor any changes in the pressure, which would indicate a leak or burst somewhere in or around the tank.
Air over the water surface in the tanks enters and exits through an air filtration system, to prevent contamination from the inlet air. Relief and vacuum valves are installed on top of the tanks to secure the tanks from damage caused by sudden changes in air pressure. A small tap is placed on each tank, for regular water quality sampling. The tanks decline slightly towards the inside of the facility, resulting in a self-cleaning feature directing any small particles to a sump pump at the end, where they settle and can be discarded.
Keeping it natural
In Denmark, the permitted drinking water treatment only includes oxygenation and filtering, where adding chlorine is common in almost all other parts of the world. This only emphasises the need for a system where the risk of water contamination is brought to an absolute minimum.
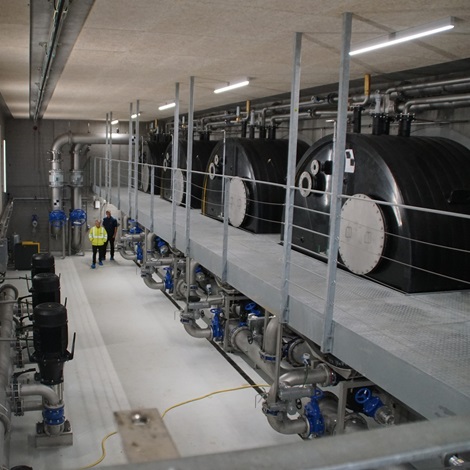
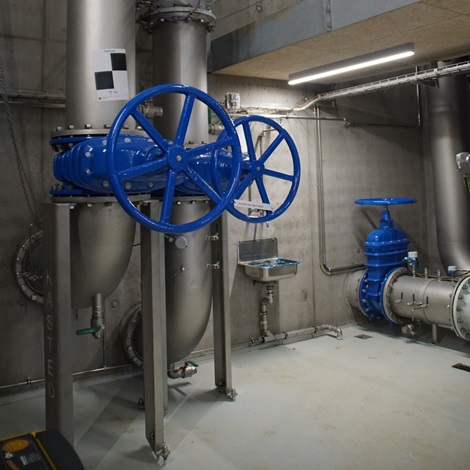
Harvesting the benefits of automation
Adding more control to the facility equipment is the main driver in reaching the goal of a demand-based supply. Before, outswings in demand were tackled through overcapacity, which will no longer be necessary as the facility will be able to respond to peak or off-peak hours, keeping the resources used at a minimum.
Being able to remotely monitor and regulate changes in the facility comes with other advantages. With the finalised setup, no staff will have to rush in at changes but can follow-up and adjust equipment settings from where they are situated. This saves valuable time and efforts, benefitting both staff and end-consumers.
Upholding the high quality also means installing equipment with no impact on the water it is in contact with. The facility has been equipped with two large DN400 AVK gate valves at the inlet from the pumping station, and smaller DN200 AVK gate valves and butterfly valves with actuation for both inlet and outlet of each of the six tanks.