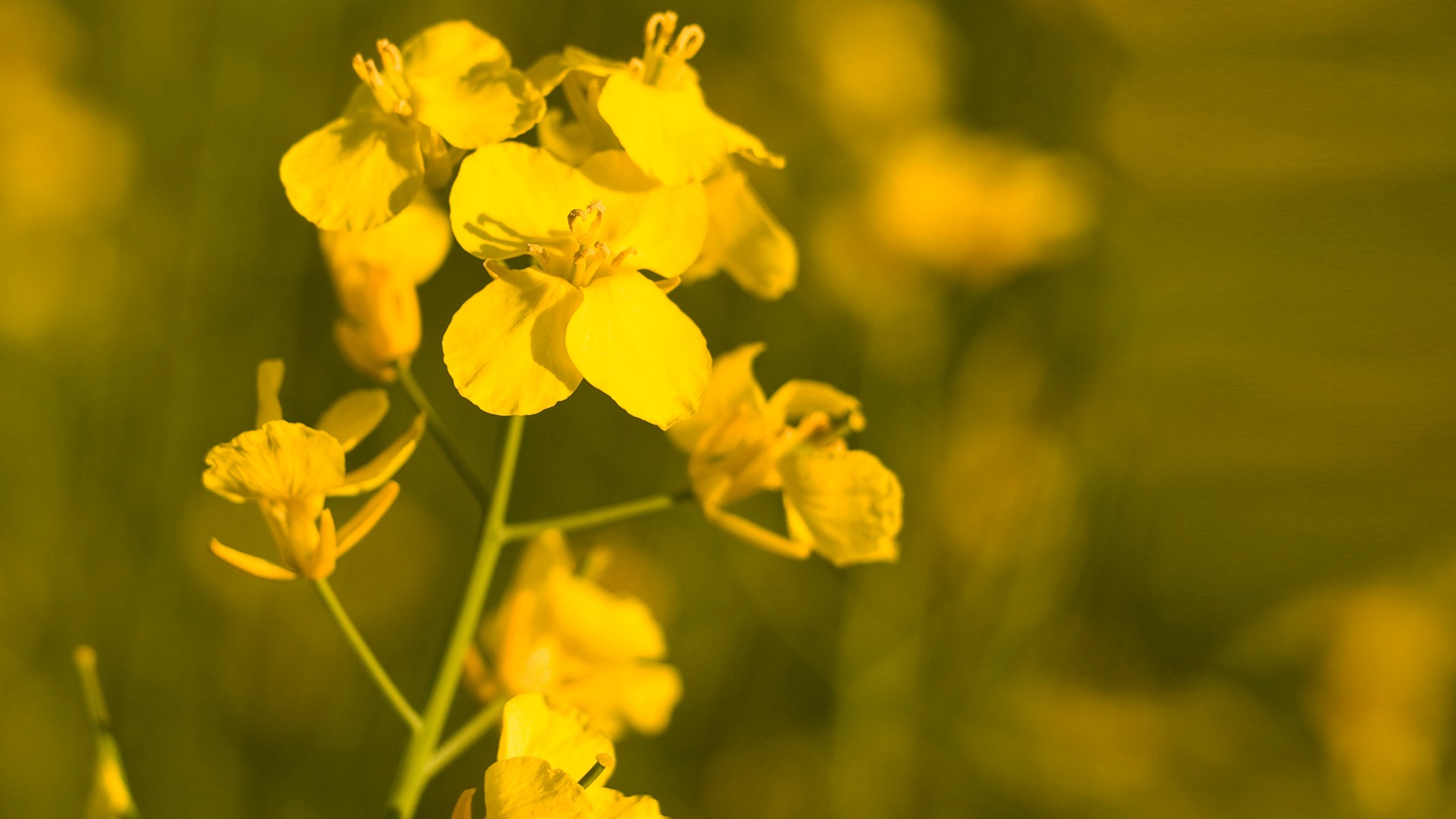
A biomass combined heat and power plant, estimated to generate as much electricity as used by 52,000 homes yearly, will supply two large pharmaceutical companies in the Northern England with power and will export excess electricity to the national grid
A renewable energy source
Biomass is a renewable and sustainable source of energy that can be used to create power, and a biomass power plant is fuelled by organic materials.
At Cramlington Biomass CHP Plant – expected to be up and running by the end of 2017 – the CO2 savings of 56,000 tonnes annually compared to a gas-fired power plant leads to a reduction of greenhouse gas emission equivalent to taking 25,000 cars off the road every year. AVK Flow Control and Tec Artec have supported the project with the delivery of the turbine bypass system for the plant.
Use of reheat technology
With the reheat technology the steam is led through two heating processes and two turbines for an increased utilisation. This improves fuel efficiency and provides a higher plant output – an advantage to both the economy and the environment. The Cramlington project will be the first reheat biomass plant in the UK.
250,000 tonnes of local wood
The plant in Cramlington will be wood-fired and fuelled from local wood provided by local growers and forest industry suppliers from an abundant local resource. There are 500,000 acres of forestry within 60 miles, and thus transforming biofuel into electricity is not only beneficial for the environment but also for the local industry and economy.
The facility is designed for a yearly throughput of nearly 250,000 tonnes of biomass expected to annually generate 223 GWh of renewable electricity. The output in the form of saturated steam heat is supplied to two large companies in the region and the remaining power will be exported to the national grid.
Turbine bypass
The turbine bypass system is a group of valves protecting the turbine in a power plant from steam not having optimal parameters. During start-up of the turbine or in case of a turbine trip, the generated steam needs to be reduced by temperature and pressure and routed to the condenser or into the reheater.
The turbine bypass system usually consists of a redundant high pressure steam shut-off and a steam pressure reducing valve with an integrated desuperheater. The desuperheater is connected to a feedwater line equipped with a water pressure reducing valve and a water shut-off valve. The Cramlington CHP Plant bypass system ends with a dump tube, consisting of several perforated discs, located upstream of the condenser.
Desuperheater
Desuperheaters are part of the turbine by pass system and there is a further demand for these in several other places in a power plant as well – also as non-integrated solutions without upstream steam pressure reduction. The main task for these desuperheaters is accurate attemperating without abrading downstream system components for every load case. This requires quick and complete evaporation which is only achieved by having a sequential opening of many small nozzles.
Unique deliveries
The Cramlington CHP plant is delivered by the Danish power plant specialist BWSC and the turbine bypass system for the plant is delivered by AVK Flow Control and TEC artec. Due to the short distance between the bypass system and the condenser, the intermediate pipe with studs for temperature and pressure measurement and the dump tube were also included in the scope of our supply.
Our turbine bypass system is made simple and optimised for durability and for a longer lifetime. Our stand alone desuperheaters provide fine spray and quick, complete evaporation. In addition, the opening by 90° rotation makes the design unique.
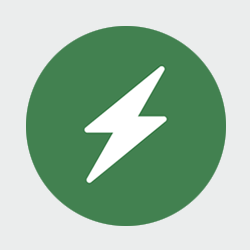
AVK solutions
Learn more about our ways of assisting in power plant projects.
Introduction to Energy Generation