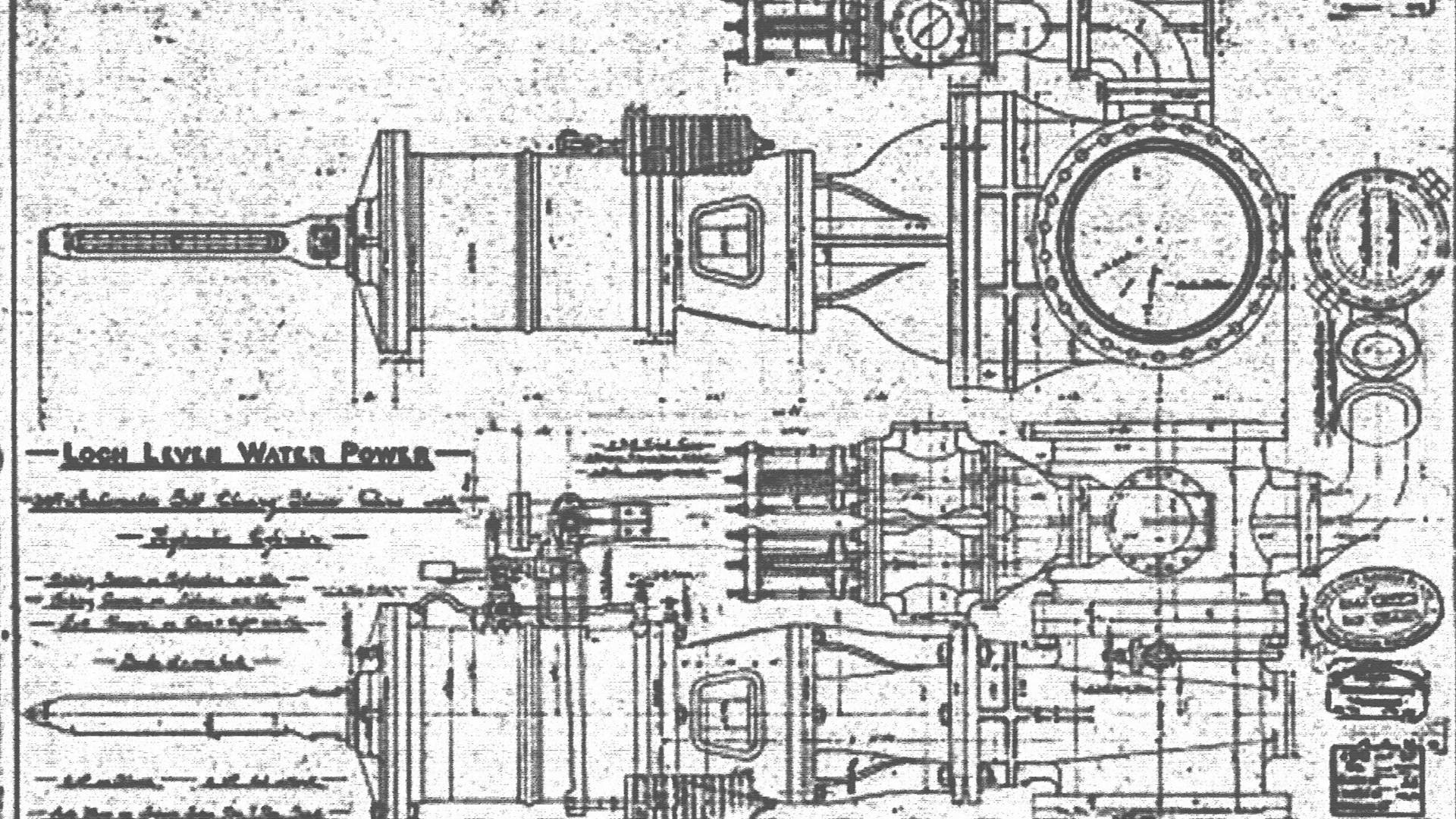
Glenfield was asked to report on the feasibility of a refurbishment program, returning 109-year-old valves to their original condition
In 2015 during a visit by Glenfield valves to Rio Tinto, one of the world’s leading global mining and metals companies, Lochaber Facility in Scotland, concern was raised over the operating function of two of the original Glenfield & Kennedy control valves. The valves in question were installed in the Kinlochleven hydropower plant during its original construction between 1907 and 1910 when the company was owned by the British Aluminium co.
Glenfield was asked to conduct an inspection of the valves to diagnose the problem and report on the feasibility of a refurbishment program to return the valves to their original condition.
Historical archive records
With access to the Glenfield extensive archive library, and with information already provided by the client which included the year of supply and the type of valve, Glenfield was able to trace the complete manufacturing details and design records of the original valves supplied over 100 years ago.
The two valves in question were 9" cast steel pressure relief valves, used to aid the operation of a 39" automatic self-closing sluice gate valve. The sluice gate, operated by a hydraulic cylinder controlled by a weight-loaded trigger, is released automatically in the event of high velocity occurring in the main line. The two pressure relief valves, which are multi-spring design, were originally fitted to the upstream side of the sluice gate to relieve the main pipeline of any excess pressure developed during the closing of the sluice valve. The pressure rating of the valves is 410 lb. per square inch (28.3 bar).
Refurbishment
With the historical valve specification retrieved from our archives, Glenfield could now provide the exact replacement components and secure the order to carry out the refurbishment of the first two pressure relief valves.
The valves were delivered to Glenfield's facility in Kilmarnock where they were disassembled and inspected. The main components were carefully shot blasted by Glenfield in-house specialists to expose the surfaces of the raw material. As anticipated, and due to the age of the valves, the original cast steel components showed signs of erosion caused by natural wear and tear over 100 plus years of operation.
On further inspection, it was determined that one of the main valve bodies had also been subjected to considerable erosion and was therefore deemed to be beyond economic repair. Utilising the historical design drawings, Glenfield was able to produce a 3D CAD model of the valve body to create a new casting pattern. The pattern was produced in the UK with the subsequent steel casting also being produced within the UK.
All of the castings were then machined to the original valve dimensions. All non-metallic components were replaced and other components, including the high pressure spring assembly, were reconditioned and returned to the required high quality standard. This included full epoxy coating of all internal and external metallic surfaces.
The valves were then reassembled and successfully hydrostatically tested to the original working pressures by experienced GVL engineers. The most important aspect of this test is to ensure that the springs are set to a specific 'blow-out' pressure to ensure the hydropower system safety.
Both valves have been reinstalled into the main pipeline and are working just as they did over 100 years ago.
Complete life cycle
This case study, without refute, demonstrates the extensive durability and life service of the original Glenfield valves manufactured and supplied over 100 years ago. It is testament to the Glenfield & Kennedy designers and employees at that time. The craftsmanship and quality of the products produced have ensured many years of successful operation and, with the level of quality and workmanship that Glenfield and the AVK Group continue to offer today, there is no reason why these valves should not provide a further 100 years of operation.
Glenfield have an unrivalled collection of historical archive information that exceeds 100 years of valve supply. As proven, this information is crucial when carrying out refurbishment work of this nature and ensures the 'new' valves continue to meet the requirements that they were originally intended for. A further ten of the same pressure relief valves are installed on this site and likely to require the same level of refurbishment within the next few years.
By Greg Morris, Engineering Manager, Glenfield Valves Ltd.
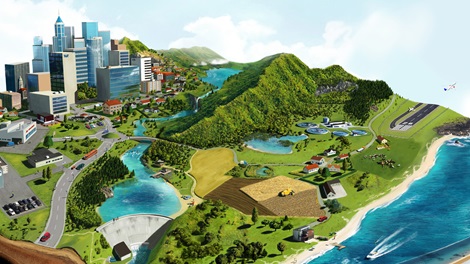
AVK solutions
Learn more about our many different ways of assisting in quality solutions.
GO TO AVK SOLUTION AREAS